Medical device testing is an essential step in the development and commercialization of medical devices, ensuring they are safe, reliable, and compliant with stringent regulatory standards. From concept validation to post-market surveillance, rigorous testing ensures that devices perform as intended, minimizing risks to patients and users. This comprehensive guide explores the intricacies of medical device testing, covering its types, methodologies, and best practices, with a focus on safety and reliability.
Table of Contents
What is Medical Device Testing?
Medical device testing involves evaluating a device to ensure it meets predefined performance, safety, and regulatory requirements. It covers every phase of the device lifecycle, including design validation, manufacturing processes, and ongoing post-market assessments.
Key objectives of medical device testing:
- Confirm compliance with regulatory standards (e.g., FDA, CE, ISO 13485).
- Validate design functionality and usability.
- Identify and mitigate risks to patient safety.
- Ensure device reliability under various conditions.
Importance of Medical Device Testing
- Regulatory Approval:
Testing is mandatory to meet the requirements of regulatory bodies, such as the FDA (21 CFR Part 820) and EU MDR. Without proper testing, a device cannot be marketed or sold. - Patient Safety:
Comprehensive testing minimizes the risk of device malfunctions, which could lead to patient harm or legal liabilities. - Product Quality:
Testing ensures consistency and reliability, which enhances user confidence and brand reputation. - Market Viability:
Well-tested devices reduce the likelihood of recalls or post-market failures, saving costs and maintaining credibility.
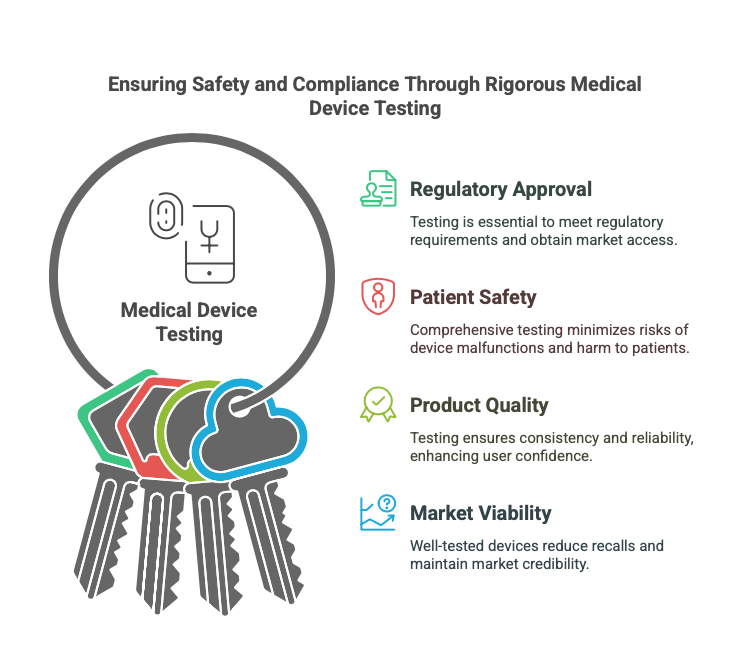
Types of Medical Device Testing
1. Design and Development Testing
This phase verifies that the device design meets intended use requirements and performance standards.
Key Tests:
- Functional Testing: Ensures the device performs its intended functions under normal and extreme conditions.
- Environmental Testing: Simulates real-world environments, including temperature, humidity, and vibration.
- Usability Testing: Evaluates user interface and ergonomic design for ease of use and error prevention.
Example:
A wearable ECG monitor undergoes functional testing to ensure accurate data capture under various patient activities, such as walking or running.
2. Biocompatibility Testing
Devices that come into contact with the human body must be tested for biocompatibility to ensure they are safe and non-toxic.
Standards:
- ISO 10993 for biological evaluation of medical devices.
Key Areas:
- Cytotoxicity: Ensures materials do not kill or damage cells.
- Sensitization: Verifies the device does not cause allergic reactions.
- Hemocompatibility: Ensures compatibility with blood.
Example:
A surgical implant is tested for compatibility with body tissues and fluids to prevent adverse immune responses.
3. Electrical Safety Testing
Electrical devices must comply with IEC 60601 standards for medical electrical equipment.
Key Tests:
- Leakage current testing to ensure patient safety.
- Dielectric strength testing for insulation durability.
- Electromagnetic compatibility (EMC) testing to assess interference with other devices.
Example:
An infusion pump undergoes EMC testing to ensure it functions correctly in hospital environments with numerous electronic devices.
4. Software Validation
For devices with embedded software, rigorous testing ensures functionality, accuracy, and cybersecurity.
Key Aspects:
- Validation of software algorithms.
- Testing for reliability under various operating conditions.
- Cybersecurity testing to protect patient data.
Example:
A diagnostic app integrated with a handheld ultrasound device is tested for accuracy in rendering images and secure data transmission.
5. Sterilization and Packaging Testing
Devices that are sterile or packaged for sterility maintenance require specialized testing.
Key Tests:
- Sterilization validation to confirm the efficacy of sterilization methods.
- Packaging integrity testing to ensure sterility during transport and storage.
Example:
A catheter package undergoes burst testing to ensure its seal remains intact under pressure.
6. Mechanical Testing
Mechanical tests evaluate the physical properties and durability of devices, especially those subjected to stress or motion.
Key Areas:
- Tensile and compression testing for material strength.
- Fatigue testing to assess durability over repeated use.
- Drop testing to simulate impacts during transportation.
Example:
Orthopedic implants are subjected to fatigue testing to ensure they withstand years of use under varying loads.
7. Clinical Testing
Clinical testing ensures that the device is safe and effective in real-world applications.
Phases:
- Pilot studies for preliminary safety assessments.
- Clinical trials to gather statistically significant data.
Example:
A glucose monitoring device undergoes clinical testing in diabetic patients to validate accuracy and ease of use in daily life.
Medical Device Testing Standards and Regulations
1. ISO 13485:
Specifies requirements for quality management systems in medical device manufacturing.
2. ISO 14971:
Focuses on risk management for medical devices.
3. IEC 60601:
Applies to electrical medical equipment safety and performance.
4. FDA Guidelines:
Regulates premarket approval and post-market surveillance in the U.S.
5. EU MDR:
European Union regulations emphasizing device safety and performance.
Challenges in Medical Device Testing
- Evolving Regulations:
Constantly changing standards require ongoing updates to testing protocols. - Complexity of Devices:
Modern devices integrate electronics, software, and materials, complicating testing processes. - Time and Cost Constraints:
Comprehensive testing can be time-intensive and expensive, particularly for startups. - Global Market Requirements:
Devices intended for international markets must meet diverse regulatory standards.
Best Practices for Medical Device Testing
- Develop a Robust Test Plan:
Outline objectives, methods, and criteria for each testing phase. - Engage Experts Early:
Collaborate with testing labs and regulatory consultants during development. - Leverage Simulation Tools:
Use advanced software to simulate testing scenarios, saving time and costs. - Document Everything:
Maintain thorough records of test results, methodologies, and compliance to facilitate audits. - Iterate Based on Results:
Use test data to refine designs and address issues before proceeding to the next phase.
Future Trends in Medical Device Testing
- Digital Twins:
Virtual models of devices used for testing performance in simulated environments. - AI in Testing:
AI algorithms analyze test data to identify patterns and predict failures. - Automated Testing Systems:
Robots and automated systems streamline repetitive testing tasks, improving efficiency. - Real-World Evidence:
Leveraging post-market data to validate and improve device performance.
Conclusion
Medical device testing is a cornerstone of developing safe, reliable, and effective healthcare solutions. By adhering to rigorous testing protocols, leveraging advanced technologies, and staying compliant with evolving regulations, medtech companies can bring transformative devices to market with confidence. While challenges exist, a systematic approach to testing ensures patient safety, enhances product quality, and strengthens market credibility.
At OVA Solutions, we specialize in guiding medtech innovators through the entire testing process, from design validation to post-market surveillance. With expertise in regulatory compliance, risk management, and advanced testing methodologies, we help you bring your vision to life while ensuring the highest standards of safety and reliability.
Need help with medical device testing? Contact OVA Solutions today to streamline your path to compliance and market success!