Surgical robot control systems represent a cornerstone of modern medical technology, enabling unprecedented precision in minimally invasive procedures. This comprehensive guide explores the latest advancements, optimization strategies, and critical considerations in developing and maintaining these sophisticated systems.
Table of Contents
Understanding Surgical Robot Control Architecture
Core Components
Modern surgical robot control systems integrate multiple sophisticated components working in harmony. The primary elements include:
- Master controllers operated by surgeons
- Slave manipulators performing surgical tasks
- Real-time feedback systems
- Motion scaling and tremor filtration processors
- Safety monitoring subsystems
Control Hierarchy
The hierarchical structure of surgical robot control systems typically encompasses three distinct levels:
- High-level supervisory control managing surgical workflow and safety protocols
- Mid-level control handling trajectory planning and coordination
- Low-level servo control ensuring precise actuator movements
Advanced Control Strategies
Haptic Feedback Integration
Surgical robot control systems with haptic feedback provide surgeons with crucial tactile information during procedures. Implementation requires:
- High-frequency force sensors
- Low-latency data processing
- Accurate force rendering algorithms
- Stable bilateral control loops
Adaptive Control Methods
Modern surgical robot control systems employ adaptive control techniques to maintain precision across varying operating conditions:
- Dynamic parameter estimation
- Real-time compensation for tissue deformation
- Automatic adjustment of control gains
- Learning-based control adaptation
Safety and Reliability Optimization
Redundancy Implementation
Multiple layers of redundancy ensure reliability in surgical robot control systems:
- Sensor redundancy for critical measurements
- Computational redundancy in control processors
- Mechanical safety stops and limits
- Backup power systems
Fault Detection and Recovery
Robust fault management systems incorporate:
- Real-time monitoring of system parameters
- Predictive maintenance algorithms
- Automated fault isolation procedures
- Graceful degradation protocols
Precision Enhancement Techniques
Motion Scaling
Precise motion scaling enables microsurgical capabilities:
- Adjustable scaling ratios (typically 3:1 to 5:1)
- Nonlinear scaling for different operation phases
- Selective scaling for specific degrees of freedom
- Adaptive scaling based on surgical context
Tremor Filtration
Advanced filtering algorithms remove unwanted motion:
- Adaptive Kalman filtering
- Wavelet-based tremor separation
- Machine learning-based motion prediction
- Real-time frequency analysis
System Integration and Optimization
Communication Architecture
Optimal system performance requires:
- Ultra-low latency networks
- Deterministic communication protocols
- Redundant data pathways
- Robust error handling
Performance Metrics
Key performance indicators include:
- Position accuracy (typically <0.1mm)
- Motion smoothness
- System latency (<10ms)
- Force feedback fidelity
Future Developments
AI Integration
Artificial intelligence enhances control systems through:
- Automated surgical planning
- Real-time decision support
- Adaptive control optimization
- Predictive maintenance
Cloud-Based Solutions
Emerging cloud technologies enable:
- Remote system monitoring
- Performance data analytics
- Collaborative surgical planning
- System updates and optimization
Regulatory Compliance and Validation
Safety Standards
Critical compliance requirements include:
- IEC 60601-1 medical device safety
- ISO 13485 quality management
- IEC 62304 software lifecycle processes
- ISO 14971 risk management
Validation Protocols
Comprehensive validation encompasses:
- Performance testing under various conditions
- Long-term reliability assessment
- Safety feature verification
- Human factors evaluation
Maintenance and Calibration
Regular Calibration
Maintaining system accuracy requires:
- Geometric calibration procedures
- Force sensor calibration
- Motion scaling verification
- Safety system testing
Preventive Maintenance
Optimal system performance depends on:
- Regular component inspection
- Software updates and patches
- Performance trend analysis
- Proactive component replacement
Conclusion
Optimizing surgical robot control systems requires a comprehensive approach encompassing advanced control strategies, safety mechanisms, and rigorous maintenance protocols. As technology continues to evolve, integration of AI and cloud-based solutions will further enhance system capabilities, while maintaining focus on precision, reliability, and patient safety remains paramount.
References
- Journal of Medical Robotics Research
- IEEE Transactions on Medical Robotics and Bionics
- International Journal of Computer Assisted Radiology and Surgery
- Medical Image Analysis
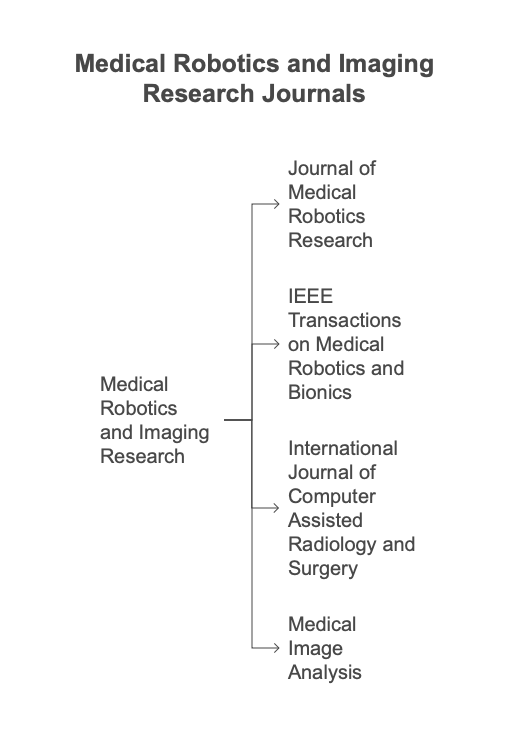